Crusher jamming is a common issue during operation that can cause both time and economic losses. Here are some effective strategies to prevent crusher jamming:
Lubrication Oil Issues
Improper Lubrication: Using insufficient, excessive, or contaminated lubrication oil can affect the equipment's lubrication effectiveness. This may lead to reduced equipment speed and crushing efficiency, resulting in material accumulation in the crushing chamber and causing blockages.
Wear and Tear of Consumable Parts
Component Wear: Worn-out parts can lead to larger particle sizes of the crushed material. During the screening process, this can cause uneven discharge and increase the risk of jamming.
Excessive Feeding Speed
Overfeeding: If material is fed too quickly into the crusher, the machine may not have time to process it adequately. Uneven or rapid feeding can cause material to accumulate in the crushing chamber, leading to severe blockages.
Clogged Discharge Opening
Discharge Obstruction: Crushers are often installed at a height with conveyors underneath. If material accumulates excessively on the conveyor below, it can obstruct the normal discharge of the crusher.
Screening Mesh Issues
Rust or Blockages: Rust or clogging of the screening mesh below the crusher can slow down discharge, leading to blockages in the machine.
Unstable Voltage
Voltage Fluctuations: Unstable voltage can prevent the crusher from reaching its normal operating speed, increasing the likelihood of jamming.
Oversized Material
Large Material Size: Processing oversized material can cause excessive wear on various components of the equipment. Over time, this can lead to blockages.
When jamming occurs, immediately stop feeding material, cut off the power supply, identify the cause of the blockage, and address it. Proper use and regular maintenance are crucial to ensure the crusher operates effectively and efficiently.
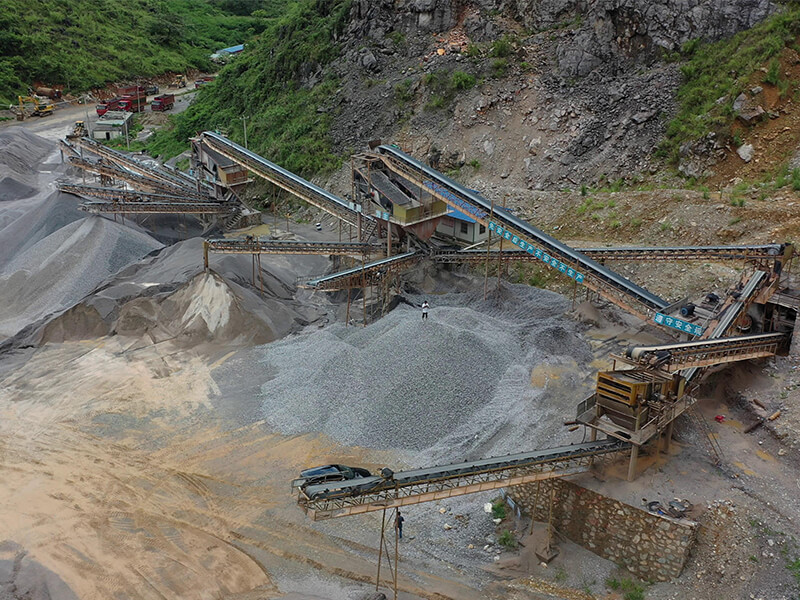
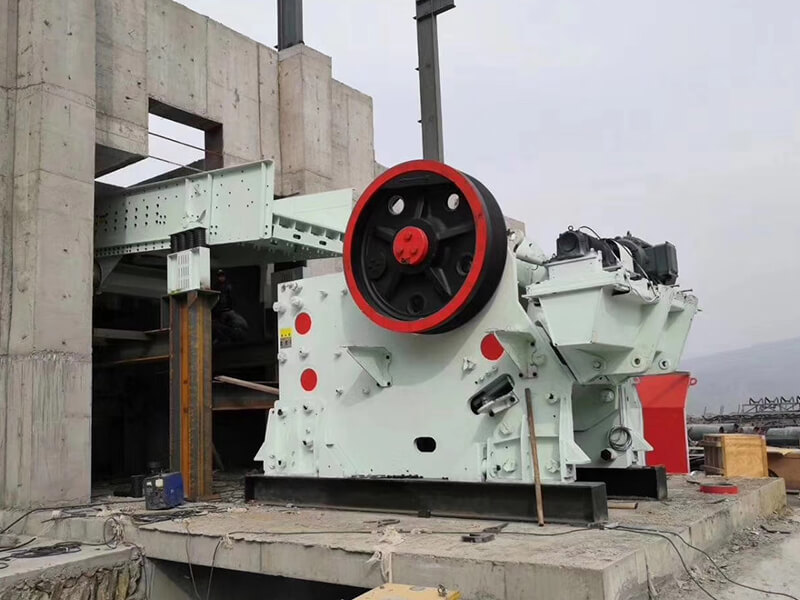